There are news about the Aerospike project from Josefine Lissner, Hyperganic Group and AMCM GmbH: The Austrian software manufacturer CADS Additive succeeds in preparing the print data in a record-breaking short time.
Since January 2023, the first “One small step for a man” is one step behind. This step takes only 8 minutes, but it opens up a completely new dimension of time – both in aeronautics as well as in many other fields. As it is with the small steps that are of great significance for mankind.
How It All Began: The First 3D Printed Aerospike
Hyperganic and AMCM took an incredibly big step for aero technology in May 2022 with Josefine Lissner’s Aerospike design. News of her 3D printed Aerospike were spread around the world. As the largest rocket engine of its kind ever successfully produced in a 3D printer, it quickly became a manifesto for a new era of possibilities in aerospace technology.
More importantly, it proved that the advancement of complex, one-piece metal parts no longer stops at production.
“The Aerospike is a true first of its kind, as it is the first and largest ever 3D-printed rocket engine of this type that was fully designed through computer code and algorithms – with no manual CAD drawing involved. It marks the beginning of a paradigm shift in engineering: On my laptop, I can generate a new variant of this engine about every 30 minutes, while the complexity of the geometry results in many GBs of output data that used to easily break most print-processing software.”
Josefine Lissner, CEO and Founder, former Strategic Engineering Lead at Hyperganic Group
Top Performance of Engineers as well as Hardware and Software
Until its completion, the Aerospike went through the same process steps as any other 3D printed part – except some special features. The Aerospike was designed using innovative algorithms without any manually created CAD data. An achievement that shrinks the design time for highly complex components to an entirely new and incredibly small dimension.
However, this was not previously the case for the data itself. Countless windings inside the part ensure that the Aerospike performs exactly as it should in practice. And that is precisely what presents the hardware and software with challenges of galactic extent. In particular, preparing these enormous amounts of data demanded time-consuming peak performance from the build processor.
Until the software manufacturer CADS Additive took a new step.
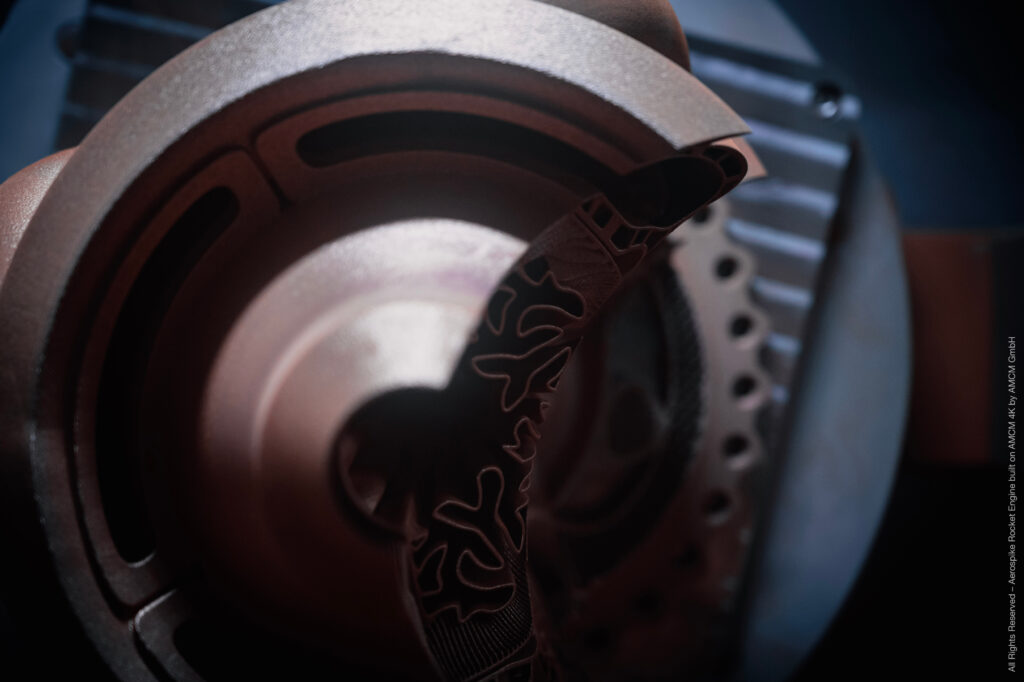
10 … 9 … 8 Minutes Preparation Time for the World’s Largest 3D Printed Aerospike
CADS Additive was also excited by the world’s largest 3D printed Aerospike – and felt challenged. The complex geometry seemed to be the ideal task for their novel build processor Titan.Core.
Titan.Core is based on innovative algorithms that significantly reduce load on working memory during slicing and hatching. As a result, print data can be prepared up to 30 times faster compared to other build processors, even on conventional workstations. Even the simulation of geometries before printing can be done quickly and efficiently, which is why CADS Additive’s complete software solution AM-Studio includes Finite Element warpage simulation as standard.
But does this also apply to components as complex as the Aerospike? How long would Titan.Core take to slice and hatch their structures?
It was an experiment that also piqued Aerospike designer Josefine Lissner’s curiosity. She provided CADS Additive with the geometries for the experiment.
The software manufacturer’s team used a standard workstation with up to 3.7 GHz and 64 GB RAM for data preparation. On this, the build processor sliced and hatched the data with impressive results:
After just 8 minutes and 11 seconds, Titan.Core was ready to transfer the print data to the 3D printer. The available RAM was not even close to being exhausted with a load of just 4 GB.
“Geometries for 3D printing are becoming increasingly complex and the build chambers of 3D printers larger. To prevent data preparation, especially slicing and hatching, from reaching prohibitive levels, we developed Titan.Core. When I first saw the Aerospike at the Rapid + TCT in Detroit back in 2022, I immediately thought of it as exactly the type of part we developed Titan.Core for. The results generated reasons for the fact that the development was worthwhile.”
Peter Leitner, Technology Specialist at CADS Additive
This achievement also impresses Josefine Lissner. The combination of her algorithms for CAD design and the powerful Titan.Core build processor allows the production of the most complex parts in fractions of the time previously required. This fact opens up completely new opportunities for research and development. For aeronautics and, of course, for all other industries.
“CADS Additive has achieved a true leap with their new slicer technology. Processing the original Aerospike geometry within 8 minutes demonstrates an improvement of an order of magnitude. This is encouraging to see and paves the way for novel, exciting engineering designs that approach the complexity of nature. We need to dramatically lift the software performance across the entire Additive Manufacturing industry and we are seeing the right steps here.”
Josefine Lissner, CEO and Founder, former Strategic Engineering Lead at Hyperganic Group
New Opportunities for Engineers and Designers: Most Complex Parts on Standard Hardware
And that is exactly the goal of CADS Additive: Software that puts developers at ease. With the Austrian software manufacturer’s solutions, designers and engineers are able to concentrate entirely on their part. Not the software or the data itself.