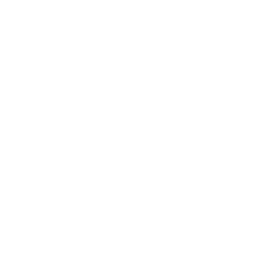
AM-Studio is an intuitively-operable high-end additive manufacturing solution which guides the user step-by-step through the entire manufacturing process – including the post-processing. Highly-developed algorithms and automatisms support the analysis of components, the creation of support geometries as well as during slicing and hatching.
Comprehensive Additive Manufacturing Solution for Novices, Advanced Users and Pros
Regardless of whether you are taking your “first baby steps” as a novice to the theme of 3D printing or, as a total pro, wanting to test the limits of what is possible additively – AM-Studio is a tool which can be used to substantially reduce the “time-to-print” for each application. Based upon the respective need, this software is available as a stand-alone solution, as a version which can be seamlessly integrated into PTC Creo® or as a special version which can be customized to a specific industry.
Easy
Operation
High-End with Regards to Diverse Functions, But Nonetheless Easy to Operate
AM-Studio is an extremely top-class data processing software for additive manufacturing which, despite its unique diversity of functions, remains easy to use even for novices to the theme of 3D printing. The users are guided step-by-step through the manufacturing process beginning from the importing of the data as well as during the selection of materials, the manufacturing machine and the zero-point clamping system which extends even to the post-processing.
Moreover, a self-explanatory graphical user guide as well as algorithms and automatisms running in the background support goal attainment. Accordingly, the centerpiece of this comprehensive additive manufacturing solution is formed by a high-end build processor whose numeracy capabilities can handle even the most complex geometries in record time – and with minimal resource requirements. For the slicer/hatcher, a hard disk capacity of at least 10 GB and memory of 2 GB are recommended. AM-Studio itself even comes equipped with 16 GB of memory. However, it is recommended to have double this memory. You can find additional details on the system requirements here.
Automated
Processes
A Software which Thinks Along with You
Many things which had not even been considered at all with comparable software solutions or which otherwise have been provided maximally as a fee-based add-on has been integrated in a standard fashion to AM-Studio – first and foremost, a healing function which repairs damaged STL files in a fully-automated fashion as well as an anticipatory pre-deformation tool which determines via a finite element calculation how “contorted” a part must be intentionally printed so that it ultimately comes out of the machine satisfying the respective requirements. An additional special feature in AM-Studio encompasses the AM-LOCK configurator, by means of which a segmentation of the building panel can be made which satisfies the respective requirements.
AM-LOCK is a zero-point clamping system from our cooperation partner pL LEHMANN which can be used throughout the entire manufacturing process – during the preparatory phase as well as during the actual 3D printing and all subsequent steps such as machining, Hirtisation® or also measuring. The digital basis for this cross-domain interaction is provided in AM-Studio. If, for example, a removal of support structures while using chemical, dynamically-electrochemical as well as hydrodynamic processes is planned, then this full-automated running post-processing method called Hirtisation is already included in the data preparation as a design rule. The digital basis for this cross-domain interaction is provided in AM-Studio. If, for example, a removal of support structures while using chemical, dynamically-electrochemical as well as hydrodynamic processes is planned, then this full-automated running post-processing method called Hirtisation is already included in the data preparation as a design rule.
Intelligent algorithms which support 3D nesting, i.e. an optimal usage of the assembly space available in the printer, are likewise offered by AM-Studio. In this context, so-called OrientationMaps signal whether the selected arrangement is, subject to the consideration of the selected preference – construction time, support volume or the thermal warping to be expected – lies more in the green or the red zone. Thus, it is made very easy for even inexperienced users to find the perfect “pole position” for the respective printing order.
Innovative
Support Geometries
Popular Standard as well as Sophisticated Special Supports to Choose From
More than that which is customary on the market, AM-Studio also has a lot to offer in the support library. In addition to the popular Block, Rod and Line support geometries, two additional special supports are provided, by means of which essential savings can be obtained with regards to construction time and materials: The Tree support and the AdaptiveCell support. With regards to the former, the support materials are structured vertically like a tree and branch out where it becomes necessary to do so. The latter works with triangles which initially are kept as big as possible in order to “obtain” construction time and which then become smaller and smaller the closer one comes to the component geometry.
If the user wishes to move from one support model to another support model or modify the features of the support geometry that has been selected, merely a couple of mouse clicks suffice and everything is automatically brought to the desired status. The supports can be modified associatively. That means: If one point is adjusted, then everything is accordingly adapted. Even subsequent changes in the Design Divisions can be depicted via mouse click during all subsequent processes. By using the “Via the “Regenerate Active Model” function, the support geometry can be re-calculated and adapted to the revised geometry. That functions in an extremely high-performance and fast manner. As an additional feature for alleviating work loads for AM-Studio users, this software contains a function called “Decision Tree”. Behind this function, there lies an Artificial Intelligence which can also be learned for each part to be manufactured and accordingly is able, after several repetitions, to recommend the “right” support in a fully-automated fashion. Thus, the “time-to-print” is substantially reduced. A savings in materials of approx. 30 % promises an additional innovative self-development from CADS Additive – namely the algorithmic support. This ensures in a fully-automated fashion that exclusively more support structure is constructed in those places where it is also actually needed owing to poorer heat transport or an acute “looming risk”.
CUSTOMER REFERENCES
AM-Studio was the success factor for us after two years of trial and error. Since the changeover, we can control our SLM and hybrid processes safely and reproducibly and have been able to increase our quality by 400 %.
Additech is a provider of end-to-end additive manufacturing solutions. Our end-to-end solutions include design, production, finishing, testing and validation. We use AM-Studio as our build preparation software for PBF, as it has a fast and easy-to-use workflow with a lot of freedom when it comes to support generation.
Using AM-Studio, machine-specific properties can be applied to series production. The simple process-oriented data preparation facilitates the procedure and we can concentrate on the essential design of the components.
A very comprehensive and helpful tool for our data preparation. Noticeably strong performance for large and/or complex data.
One of the biggest challenges in the entire SLM process lies in data preparation - component location, distortion, support structures, pressure parameters, ... – all these challenges must be solved with software support. AM-Studio is the perfect tool and guides us intuitively through the individual process steps of data preparation.
The right software is the first step to high-quality and repeatable components in the complex AM process chain.
AM-Studio has an excellent UI, and in addition to the fact that support design can be performed accurately and easily according to the required content, the flow from data import to the cleanup of modeling data is easy to understand. By changing the parameters of the support, powder collection became easier, what also improved post-processing labor. Further, molding time was reduced by the hour, not the minute, and the molding schedule was restructured.
The overall improvement of AM, from design to post-processing, as well as the improvement of the cost of modeling, was significant. As a result, we had a sense of trust in the software.
FAQ
Questions & Answers
- Operating System: Windows 10 or Windows 11 (64 bit)
- CPU: Intel Core i7 or the equivalent
- Memory: 16 GB (32 GB recommended)
- Graphic card: 4 GB memory (8 GB recommended) supports DirectX 11+, Shader Model 5.0+, Vulkan API, OpenGL 4.3+ (e.g. nVidia geForce GTX 1070 or similar)
Check the settings in order to see whether you have activated the auto check, auto heal or activate collision module settings. These functions require more loading time – whereby the first option is recommended.
All slice/hatch results land there – and indeed in a subfolder which has the same name as your project. If you do not assign a name, the results will be stored in the Unsaved Project directory.
Press Strg + S in order to save your project. Afterwards you can restart the software and load your project as well as continue to work precisely at the point before the “freeze”.
They are deleted as the result of diverse manipulations in order to guarantee that you are not workign with altered data. If you would like to export the STL, use the Export function for this.
Please check that you have acquired the CAD Interface and, if yes, check in the settings that CAD interface has been ticked.