3D metal printing lets you produce very complex parts that have impressive structural performance while also being completely unique. However, it is usually relatively expensive to print an individual part. This is because, unlike traditional mass manufacturing techniques which become cheaper the more you produce, the creation of individual 3D metal parts will always be time and energy intensive. You can’t just continually reuse the same mould to produce thousands of identical widgets.
In this blog, we will look at the common costs of 3D metal printing, then explore some of the ways that you can reduce your outgoings.
What are the main costs of 3D metal printing?
To get an idea of the costs of producing a 3D metal part, you need to consider both the manufacturing and the post processing stage. The exact cost of each part will of course vary depending on its size and complexity.
Nonetheless, it is possible to start to get a ballpark figure for the general costs of 3D metal printing, which you can then apply to your own designs. The following table, using data from the 3D Hubs website, will help you get an idea of the costs involved in producing a standard build plate of between 6 and 12 parts.
3D printing | Material cost | $ 175.00 | 8.05 % |
DMLS/SLM cost | $ 375.00 | 17.24 % | |
Post-processing | Stress relief | $ 68.75 | 3.16 % |
Part/supports removal | $ 150.00 | 6.90% | |
Heat treatment/HIP | $ 156.25 | 7.18 % | |
CNC machining | $ 1,250.00 | 57.47 % | |
Total | $ 2,175.00 | 100.00 % |
As the table shows, there are two areas in particular which contribute to almost three quarters of the total cost of printing a metal 3D part. These are:
CNC machining
All 3D printed metal parts must undergo post processing. This typically involves the use of software controlled machinery and skilled machine workers who will require between a few hours and a couple of days to finish each part. The work involves removing each part from its base or support structure, polishing it and turning it into a ready to use widget. CNC machining includes the cost of the energy used in processing the part, but also staff salaries.
DMLS/SLM
Direct metal laser sintering (DMLS) and selective laser melting (SLM) refer to the costs of using the 3D printer itself. A metal 3D printer uses a significant amount of energy, so the longer that the printing job takes, the higher this cost will be. Larger, more complex jobs will of course cost you more money.
Learn more: 6 major cost factors in 3D metal printing
How to bring down 3D metal printing costs
Although 3D metal printing will never be ‘cheap’, there are a number of things you can do to reduce the costs involved in using this method. These include:
Reduction of machine costs in 3D metal printing
The best way to reduce the cost of ownership of your DMLS or SLM machine is to reduce the time it takes to 3D print the part. For example, 3D metal printing might allow you to produce dental parts that are completely unique to each patient. By using software that can automate design, you can speed up this process significantly. On a dental part, much of the fundamental geometry is identical; you will still need to customise certain elements to the patient’s mouth, yet most of the work is already done for you. The part’s orientation, support structure generation, placement and slicing and matching can be repeated from one design to next. Your designer can then simply make a couple of tweaks to an existing design file without having to continually rebuild from scratch.
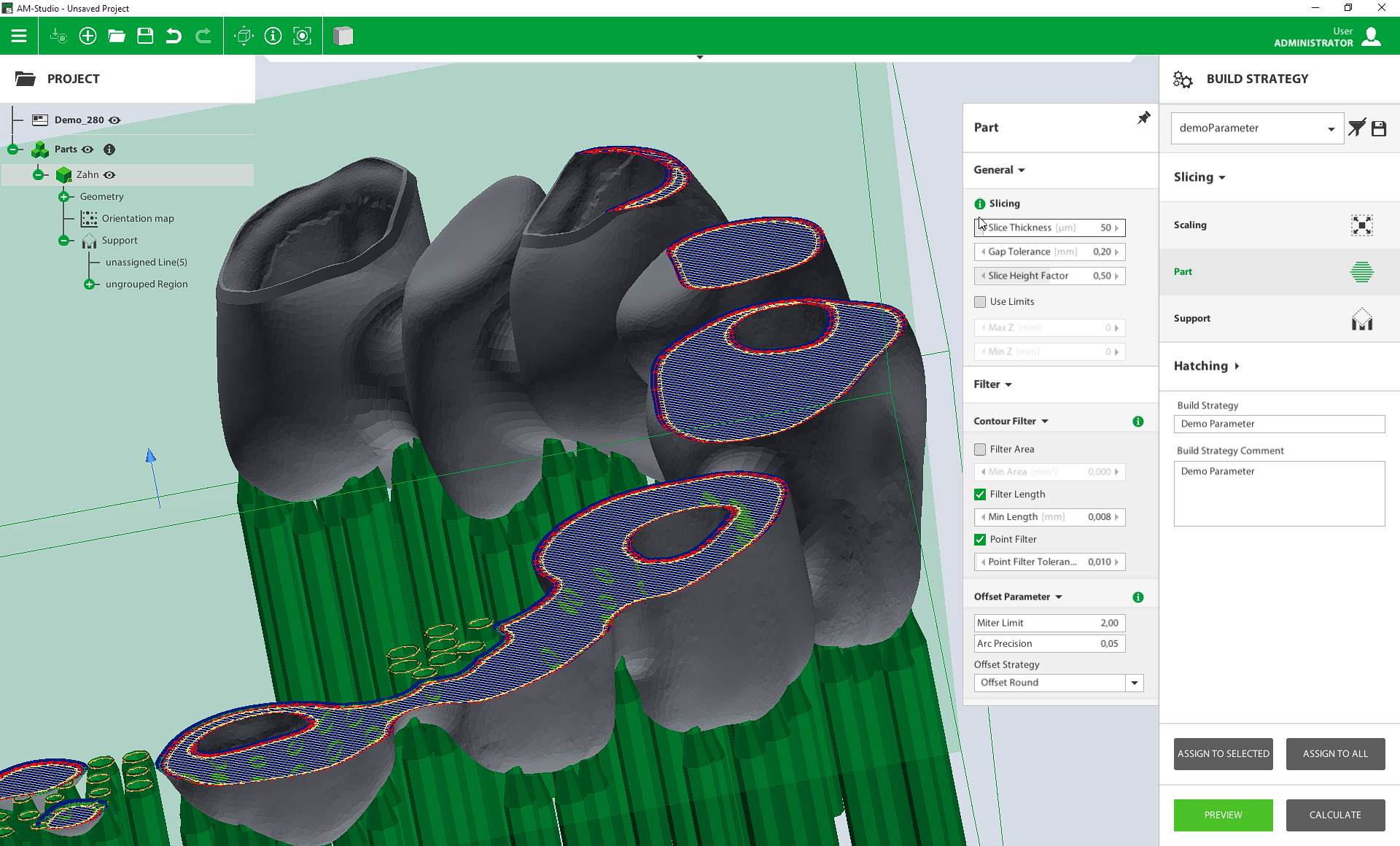
Cutting the CNC finishing costs of 3D metal printing
CNC machining costs are by far the largest cost component of a 3D metal piece. After all, it takes software-controlled machines and machinists to turn a “raw” 3D-printed part into a polished as well as ready-to-use part.
Most 3D printed workpieces come out of the machine with support structures. It takes experienced workers several hours to structurally remove these elements. The combination of technology, man-hours required and energy makes this the most expensive process step.
There are several emerging techniques that help to reduce the amount of time your teams spend on CNC finishing. Recent research shows that using supports that can be dissolved in acid can cut post processing time from a matter of days to just a few hours. Furthermore, some SLM editing software can help you design ways of removing support structures with greater ease.
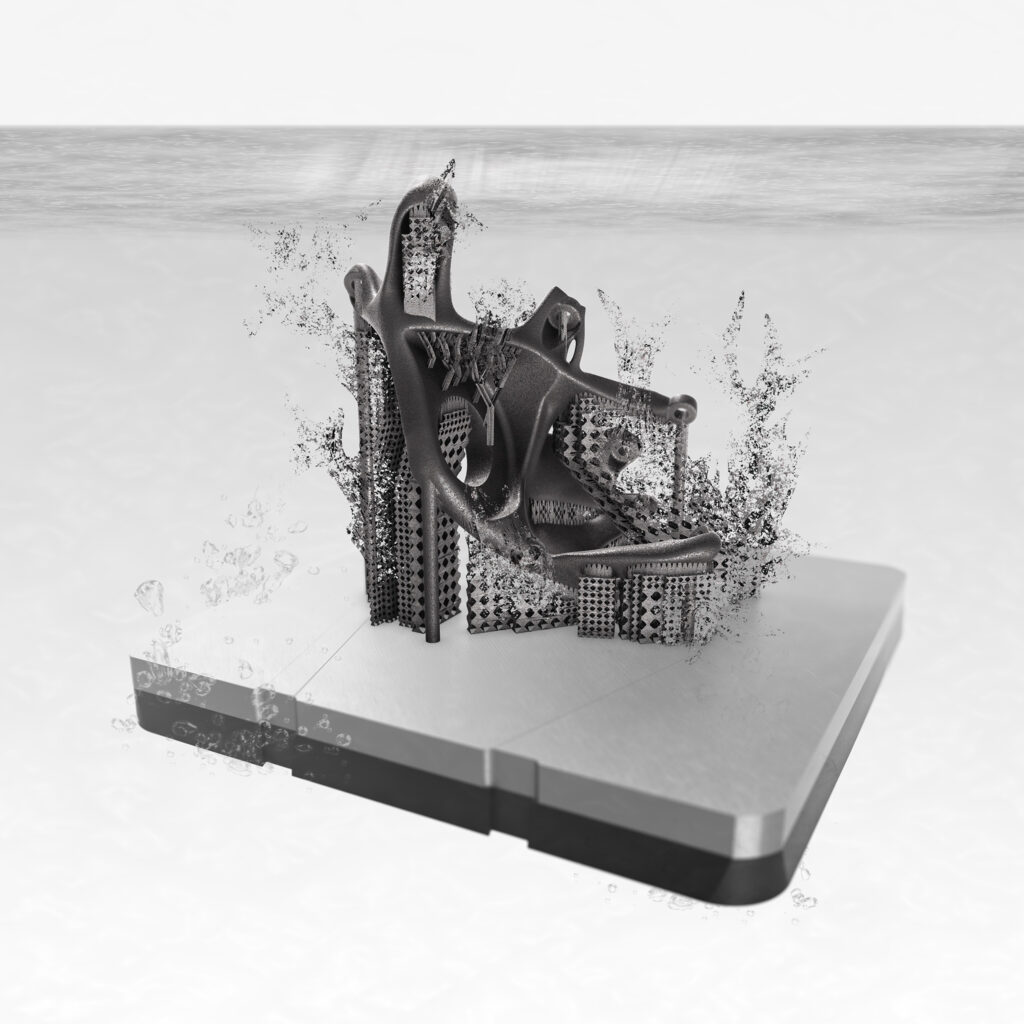
Stay on the ball: advantages and disadvantages of metal printing
Reducing design time through automation
The beauty of 3D printing metal parts is that it allows you to produce completely unique and customized pieces. This would typically mean that each design needs to be custom built in the software – and that could take many hours of a designer’s time. However, today’s 3D metal printing software can help you to quickly increase the volume of parts you can produce by automating many stages of this process.
For example, 3D metal printing might allow you to produce dental parts that are completely unique to each patient. By using software that can automate design, you can speed up this process significantly. Built-in machine libraries and pre-defined support structures help to speed up the data preparation of your files, design more parts and therefore boost your profits while also reducing your costs.
Optimize 3D metal printing
By finding ways to optimize your 3D metal printing processes, you can save your company significant sums of money while boosting productivity.
At CADS Additive, our mission is to find ways to automate and improve your processes around 3D printing. Our software brings you powerful and easy to use 3D metal printing design tools that help with the automation of many aspects of design. That saves your skilled workers from having to continually repeat work – and means they can produce more parts in less time.
Try CADS Additive today to see how it can help you automate the design process while reducing the cost of 3D metal printing for your business.